Arctic Cat 700 4x4 Service Manual
Posted : admin On 04.10.2019. FOREWORD This Arctic Cat Service Manual contains service, maintenance, and troubleshooting information for the 2012 Arctic Cat 700 Diesel SD ATV. The complete manual is designed to aid service personnel in service-oriented applications. When using this manual as a guide, the technician should use discretion as to how much disassembly is needed to correct any given condition. Fan.99 Adjusting Headlight.155 Taillight Assembly.
155 Water Pump. 99 Troubleshooting.99 Seat. 155 700 DIESEL SD Troubleshooting.156 Electrical System.100 Battery.100 Testing Electrical Components. 101 Switches.101 SHARE OUR PASSION. General Information CYLINDER, PISTON, AND RINGS Bore x Stroke 75 x 77.6 mm (2.95 x 3.05 in.) NOTE: Some photographs and illustrations used in Piston Ring End Gap - Installed (min) 0.25 mm (0.0098 in.) Piston Ring Groove Width (1st) 0.090-0.125 mm this section are used for clarity purposes only and. ENGINE/TRANSMISSION DRIVE TRAIN COMPONENTS Torque Torque Part Part Bolted To Part Part Bolted To ft-lb N-m ft-lb N-m Transmission Mounting Crankcase/Transmission Front Mounting Bracket Engine Plate Engine Mount (Upper).
2015 Paper Service Manuals. 2015 Wildcat Trail XT LTD White Metallic 700. 2015 XR 700 XT EFI Camo EPS 4x4 Auto. View and Download Arctic Cat 400 TRV service manual. Offroad Vehicle Arctic Cat 500 4x4 Operator's Manual. Offroad Vehicle Arctic Cat 700 EFI Service Manual.
Frame Connecting Rod Cap Connecting Rod (4 Steps) Engine Mount (Front/Rear) Frame Main Bearing Cap Engine Block (6 Steps). Torque Conversions Fuel - Oil - Lubricant (ft-lb/N-m) NOTE: Arctic Cat recommends the use of genuine Arctic Cat lubricants. Ft-lb ft-lb ft-lb ft-lb RECOMMENDED FUEL 35.4 69.4 103.4 36.7 70.7 104.7 The recommended fuel to use is biodiesel blend up to 38.1. RECOMMENDED FRONT DIFFERENTIAL/REAR DRIVE Preparation For Storage LUBRICANT The recommended lubricant is Arctic Cat Gear Lube or an equivalent gear lube which is SAE approved 80W-90 CAUTION hypoid. This lubricant meets all of the lubrication Prior to storing the ATV, it must be properly serviced to requirements of the Arctic Cat ATV front differentials prevent rusting and component deterioration. Check all control wires and cables for signs of wear CAUTION or fraying.
Replace if necessary. Connect the positive battery cable first; then the nega- 4. Change the engine oil and filter. Check the entire brake systems (fluid level, pads, 5. It is advisable to lubricate certain components periodi- cally to ensure free movement. Apply light oil to the Periodic Maintenance/ components using the following list as reference. Throttle Lever Pivot/Cable Ends B.
Brake Lever Pivot/Cable Ends Tighten all nuts, cap screws, screws, and bolts. Clean dust and debris from the air filter housing; then remove the cotton-fabric safety element using Air Filter care not to allow dirt and debris to enter the engine. CLEANING AND INSPECTING FILTER CAUTION Failure to inspect the air filter frequently if the vehicle is used in dusty, wet, or muddy conditions can damage the engine. DE015 CF105A 9. Install the air filter housing cover (drain facing 2.
Using a suitable brush, clean the carbon deposits downward) and lock it in place by turning clockwise. From the screen taking care not to damage the screen. NOTE: If the screen or gasket is damaged in any way, it must be replaced. Engine RPM (Idle) NOTE: The idle RPM is not adjustable on the 700 Diesel. Engine Oil - Filter Change the engine oil and oil filter at the scheduled inter- vals. The engine should always be warm when the oil is DE018 changed so the oil will drain easily and completely. Install the drain plug and tighten securely.
Pour rec- ommended lubricant into the filler hole. Install the filler plug. Remove the transmission lubricant level stick and wipe it with a clean cloth; then check the lubricant level with the level stick. Lights Each time the ATV is used, lights should be checked for proper function. Rotate the ignition switch to the lights position; the headlights and taillight should illuminate. Test the brakelight by compressing the brake lever. The brakelight should illuminate.
CF132A CD714A 3. Insert the socket into the housing and turn it clock- wise to secure. Shift Lever CHECKING/ADJUSTING HEADLIGHT AIM CHECKING ADJUSTMENT The headlights can be adjusted vertically and horizon- tally. The geometric center of the HIGH beam light zone is to be used for vertical and horizontal aiming. CF258A AL681 3.
Tighten the jam nuts securely; then shift the trans- 2. Compress the brake lever/pedal several times to mission to each position and verify correct adjust- check for a firm brake. If the brake is not firm, the ment. NOTE: During the bleeding procedure, watch the reservoir/sight glass very closely to make sure there is always a sufficient amount of brake fluid. If low, refill the reservoir before the bleeding procedure is continued.
Failure to maintain a sufficient amount of fluid in the reservoir will result in air in the system. Coolant When filling the cooling system, use a coolant/water mixture which will satisfy the coldest anticipated weather conditions of the area in accordance with the coolant manufacturer’s recommendations. While the cooling sys- tem is being filled, air may become trapped; therefore, elevate the rear of the ATV 30-40 cm (12-16 in.) to allow air to bleed from the filler neck. DE096A DE488 NOTE: The diesel engine in this ATV rotates coun- terclockwise as viewed from the right side; therefore, if directional arrows are printed on the V-belt, they must be directed rearward. Push the V-belt down into the driven pulley approxi- mately one inch. Place the V-belt cover gasket into position; then install the cover and secure with the cap screws. Tighten to 9 ft-lb.
Depress and release the manual primer pump to charge the fuel filter and purge any air from the sys- tem. Unit Injector Retainer Nut Tool 0444-227 Pre-Combustion Chamber Ring Nut Tool 0444-235 NOTE: Arctic Cat recommends the use of new gas- kets, lock nuts, and seals and lubricating all internal Pre-Combustion Chamber Removal Tool 0444-228 components when servicing the engine/transmis.
Removing Engine/ Transmission Many service procedures can be performed without removing the engine/transmission from the frame. Closely observe the note introducing each sub-section for this important information. AT THIS POINT If the technician’s objective is to service/replace left- DE066A side components, right-side components, and/or top- side components, the engine/transmission does not have to be removed from the frame. CAUTION The fuel rail connections are easily bent. Use care when removing the hose clamps and hoses. Disconnect the wire connectors from the temperature sensor, oil pressure sensor, gear position switch con- nector, and voltage regulator; then disconnect the starter solenoid, glow plug power wire, and the alter- nator positive wire.
DE494A DE086A 14. Apply the hand brake and engage the brake lever 19. Remove the cap screw and nut from the upper right lock; then remove the cap screws from the front engine mount. Account for a flat washer. Drive coupler.
Remove the transmission level stick mount and 5. Drain the transmission lubricant into a suitable con- housing; then disconnect the throttle cable from the tainer; then disconnect the transmission vent hose, throttle control arm and unthread the throttle cable gear shift position switch connector, speed sensor housing. AT THIS POINT To service any one specific component, only limited dis- assembly of components may be necessary. Note the AT THIS POINT information in each sub-section.
NOTE: The engine/transmission does not have to be removed from the frame for this procedure. SPEED GOVERNOR Removing/Disassembling 1. Disconnect the high-low speed spring assembly from the throttle control arm; then remove the intake man- ifold/throttle control housing. Account for a gasket. DE245A DE258A 5. Rotate the crankshaft in the direction of rotation approximately 90° from TDC.
NOTE: Do not loosen or remove screws (D) or (E) or fuel delivery equalization will have to be performed. DE252A DE291A DE285A DE327 DE286A CAUTION Do not break the seal or turn the torque limiter adjuster DE282 screw. Severe engine damage could occur. Inspect the control spool, thrust bearing, and thrust washer for scoring, excessive wear, or missing bear- ing rollers. DE254 Inspecting 1. Inspect the flyweight assembly for loose pins, worn DE278A contact points, or excessive pivot point wear.
Coat all serviceable parts with clean engine oil. Assembling/Installing 1. Place control spool, thrust bearing, and thrust washer into the governor flyweight assembly and secure the flyweights with a rubber band; then place assembly onto the camshaft with a new O-ring. Make sure to remove the rubber band. DE258A DE279A DE248A 4.
DE246A DE262 7. Using a new O-ring, coat the flange of the camshaft 10. Install the timing belt (see Left-Side Components in bearing retainer and the camshaft support housing this section). With clean engine oil and install into the cylinder 11. CAMSHAFT/ROCKER ARMS Removing 1. Remove the timing belt (see Left-Side Components in this section). Remove the front rack and front body; then remove the air filter assembly and mounting bracket, and air diverter with ducts.
Remove the fuel hoses from the fuel rail; then plug or close off the hoses to prevent fuel leakage. DE275A DE260C DE404A DE529 9. Place a holding pin into the injector pump barrel; 11. Using an appropriate holding tool, remove the cap then rotate the camshaft until the second injector is screw securing the camshaft drive pulley to the cam- fully compressed and install a holding pin. DE246A DE299A 13. Remove the governor control spool, thrust bearing, CAUTION and thrust washer keeping all components in order of Make sure to support the camshaft while the journals disassembly.
Are pulled clear of the journal bores or damage to jour- nal bores may occur. DE524 DE522 5.
Inspect rocker arms, camshaft followers, and rocker shaft for excessive wear, broken or scored rollers, or cracked rocker arm shaft supports. Using a micrometer, measure and record camshaft intake, exhaust, and injection lobe height.
Measure- ments must not be less than minimum specifications. Installing NOTE: If the rocker arm assembly is to be disas- sembled, label all rocker arms for installing purposes. NOTE: The flywheel end of the camshaft includes a If the rocker arms are mixed up, the complete over- bolt-on eccentric to drive the lift pump. DE540B DE535 DE530 DE536 4. Place the control spool, thrust bearing, and thrust washer into the governor flyweight assembly; then using a rubber band, secure the weights around the control spool.
Using a new O-ring, install the camshaft support housing and tighten the cap screws to 7 ft-lb. DE262 DE260C 10. Install the timing belt (see Left-Side Components in AT THIS POINT this section). If the cylinder head has been removed, no more compo- 11. Check adjustment of all valves (see Top-Side Com- nents may be installed prior to installation on the ponents in this section).
DE077B DE294A 16. Install the air filter assembly; then remove the tape 6. Remove the fuel hoses from the fuel rail; then plug from the engine air intake boot and connect the air or close off the hoses to prevent fuel leakage. Servicing Proper servicing of fuel injection components requires a number of special instruments, special training, and an extremely clean environment (clean room); therefore, Arctic Cat recommends injector service be performed by a qualified diesel injection service facility. Installing DE327 10. Remove the injection control rack by carefully disen- 1. DE565A DE567B 3.
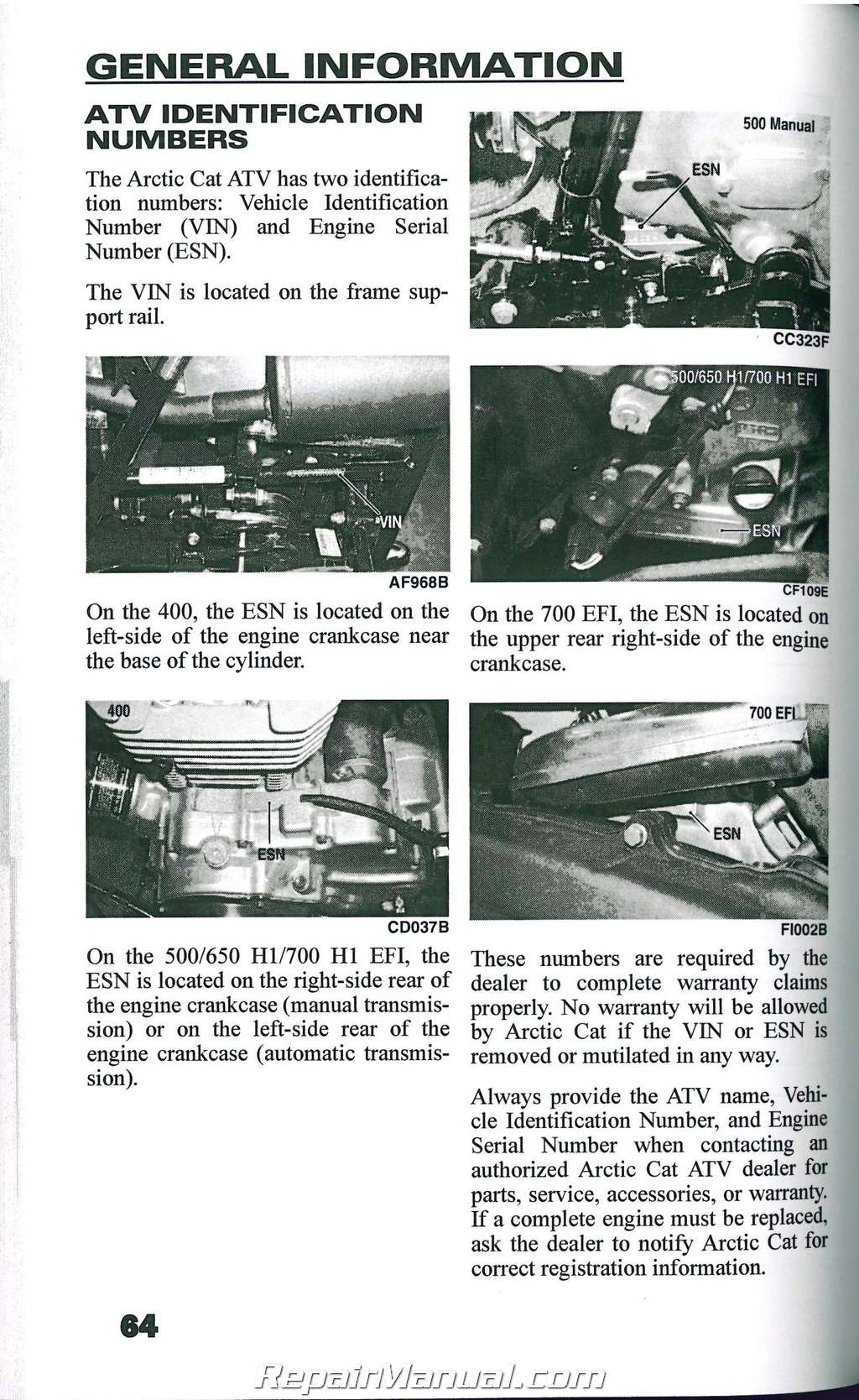
Measure the injector nozzle protrusion (A). Clean the fire ring sealing surface on the injector tip ment should be 6.80-7.05 mm (0.268-0.277 in.).
Taking care not to damage the injector tip. Excessive protrusion may be corrected by installing supplemental washers available in 0.25 mm (0.001 in.) sizes along with the standard copper washers (B). DE570 DE328 11.
Install the injector control rack by first engaging the NOTE: A small amount of lithium grease applied to governor linkage sleeve; then secure to the injection the washers will aid in keeping them in place on the pump fuel controls with the pivot screws. AT THIS POINT If injectors were serviced, static injector timing must be set (see Top-Side Components in this section). Using new O-rings, install the fuel rail and secure with four Allen-head machine screws.
Tighten to 36 in.-lb. DE405B CAUTION The valve cover and gasket are important components in the lubrication system. Rotate the engine clockwise until either cylinder is at TDC as shown in the following illustration.
2007 Arctic Cat 700 4x4 Wet Clutch
DE074A DE557A 5. Using an appropriate thickness gauge, check the clearance between the camshaft follower and cam- shaft. DE294A DE642A 6. To adjust the clearance, loosen the jam nut (A); then rotate the adjuster (B) to obtain the specified clear- ance (C).
Place a small bead of high-temperature sealant on the fuel rail seal; then carefully install the valve cover with a new gasket and oil return boot. Using a crisscross pattern, tighten the Allen-head cap screws to 6.5 ft-lb; then tighten the two “tamper-proof”. NOTE: If marks are aligned, timing is correct (pro- ceed to step 9). If marks are not aligned, the injector timing must be adjusted.
Adjust injector timing using the following procedure. Observe the position of the reference mark (D) and the 13°. Hold the adjustment screw and tighten the jam nut CYLINDER HEAD ASSEMBLY securely; then check the injector timing by repeat- AT THIS POINT ing steps 5-7. If the cylinder head or components require servicing, 9.
Remove the Fuel Injector Timing Tool and install on the engine/transmission must be removed. AT THIS POINT If the cylinder head is being removed to allow removal of engine block components, no further disassembling is required. Proceed to Cleaning and Inspecting in this sub-section. If the cylinder head is to be serviced or replaced, proceed to Disassembling in this sub-section.
CAUTION Do not attempt to remove the pre-combustion chambers before removing glow plugs. Severe damage WILL occur. DE310A DE321 7. Remove the exhaust manifold; then remove the ther- mostat housing. Cleaning and Inspecting Cylinder Head/Valves 1. Thoroughly clean the cylinder head in a non-caustic solvent. Servicing Valves/Valve Guides/ Valve Seats If valves, valve guides, or valve seats require servicing or replacement, Arctic Cat recommends that the compo- nents be taken to a qualified machine shop for servicing.
CAUTION If valves are discolored or pitted or if the seating surface is worn, the valve must be replaced. Making sure any spacers/shims are correctly installed, place the pre-combustion chamber into the cylinder head with the glow plug opening directed toward the glow plug bore. NOTE: To simplify installation/orientation of the pre- combustion chamber, install the chamber on the removal tool. DE311A DE386 5. Remove the Pre-Combustion Chamber Index Tool C.
Use steps A and B to measure and record piston and repeat steps 2-4 for the second pre-combustion protrusion on the other piston. Chamber; then install the glow plugs and tighten to D. DE341A DE577A 2. Make sure the cylinder deck surface is clean and free 5. Clean the threads of the cylinder head bolts on a wire of all oil, grease, varnish, or coolant.
Wheel; then measure the length of the bolt. Bolt length must not exceed 91 mm. Adjust the valves (see Top-Side Components in this section). Check and adjust static injector timing (see Top-Side Components in this section). Install the engine and transmission (see Installing Engine/Transmission in this section). Left-Side Components NOTE: For efficiency, it is preferable to remove and disassemble only those components which need to DE211A 6.
DE269A DE273 9. Check that the reference mark (C) on the timing belt 2.
Inspect the drive and driven pulleys for wear, burrs, drive pulley aligns with the reference mark (D) on or dirt build-up between cogs. Clean and remove the oil pump housing. Install the Timing Belt Tensioning Tool on the timing belt tensioner tab; then using a suitable torque wrench, position the handle 90° to the tensioner tab and apply 14.5 ft-lb of torque.
Tighten the timing belt idler nut securely. Remove the lower radiator hose and the coolant bypass hose from the water pump; then remove four cap screws securing the water pump and remove the water pump. Thoroughly clean all gasket material from the engine block and water pump. Remove the screws securing the oil pump to the engine block; then tap lightly on the oil pump with a plastic mallet to loosen the gasket and remove the oil pump assembly from the crankshaft. DE237 NOTE: If there is a groove worn in the crankshaft where the seal contacts, press the seal into the bore an additional 2 mm (0.080 in.). DE266A DE519B 4.
Lubricate the crankshaft and crankshaft seal with a 3. Loosen the alternator adjuster cap screw (A) and the liberal amount of engine oil; then install the oil pump pivot bolt (B); then remove the alternator drive belt. Onto the crankshaft being careful not to damage the oil seal. DE103B DE099A 3.
Holding tension on the belt, tighten the adjuster cap 3. Remove two cap screws securing the starter to the V- screw securely; then remove the pry and tighten the belt housing; then remove the starter. Pivot bolt securely. Inspecting 1.
Inspect the V-belt housing for cracks, elongated mounting hoses, or loose alignment pins. Inspect the flywheel/ring gear assembly for worn or broken teeth, cracks, or elongated mounting holes. Replacing Ring Gear To replace the ring gear, use the following procedure. DE102A DE119A 4. Remove the shift shaft housing.
Account for a gas- TRANSMISSION ket. Disassembling Gear Case 5. Remove the shift shaft, noting the match marks on the drive and driven gear plates.
Account for a 1. Remove the gear position switch. Account for two washer on each end. NOTE: For steps 10-15, refer to illustration DE663B. From the right side, remove the cap screws securing the transmission halves together; then lay the trans- DE663B 10. Remove the output driveshaft assembly (A).
Account mission on a suitable bench with the right side down. For the bearing alignment C-ring in the bearing boss next to the output driven bevel gear. DE139 DE655A 14. Remove the countershaft assembly (E).
Account for 17. Using an appropriate seal removal tool, remove any a thrust washer on each end noting the different damaged seals from the transmission case. Remove the snap ring securing the output drive bear- ing in the right-side case. DE146 DE150A 20. Remove the retaining nut from the front driveshaft and remove the front drive yoke. Account for a washer, seal, bearing, and shim. Remove the thrust washer and countershaft drive gear from the opposite end of the countershaft.
DE152 DE184 27. Remove the low gear.
Account for a washer and the low gear bearing and bushing. Remove the snap ring securing the reverse gear; then remove the reverse gear. Account for a thrust washer DE155 and the reverse gear bearing and bushing.
Inspecting 1. Inspect all shift dogs for chips, rounded dogs, worn 4. Inspect roller bearings for chipping, missing rollers, splines, or discoloration. Or discoloration. DE178 DE162 DE185 5. Inspect drive and driven bevel gears for proper tooth DE177 3.
Inspect all idler gears, bushings, thrust washers, and contact, chipping or discoloration of gear teeth, worn shafts for abnormal wear, discoloration, chipping, or or chipped splines, and bearing smoothness. Inspect shift forks for excessive wear, galling of wear surfaces, or discoloration. Inspect bearings for discoloration, flaking, or rough- ness and binding when turning. Inspect shift cam assembly for worn cam grooves or 12. Inspect and thoroughly clean all bearing pockets, broken springs. DE158B DE186 2.
Install the low driven gear onto the bearing with the 5. Install the reverse shift dog and splined bushing onto shift dog slots directed toward the fine-splined sec- the shaft; then secure with a snap ring. Tion of the countershaft; then secure with a splined washer and lock washer.
Install the high driven gear thrust washer, bushing, and bearing; then install the high driven gear and thrust washer. Place the spacer on the output shaft; then press the secondary output driven gear onto the output shaft until it firmly contacts the spacer. Install the secondary driven output shaft into the gear case and seat firmly.
Mount the dial indicator so the tip is contacting a tooth on the secondary drive bevel gear. While rocking the drive bevel gear back and forth, note the maximum backlash reading on the gauge. DE170 DE192A 3. Install the assembled countershaft assembly taking care to position a washer on each end. Install the reverse idler gear making sure to install a washer on each side of the gear; then install the input DE142 driveshaft. Install the high/low shift fork and engage the fork in the high/low cam slot in the gear shift shaft; then install the shift fork shaft. DE133D DE136A 6.
Install the secondary output driveshaft aligning the front bearing alignment ring with the groove in the gear case and rotate the bearing to locate the bearing anchor pin in the slot. Install the speed sensor trigger and secure with the circlip; then install the speed sensor housing and secure with the cap screws. Tighten securely. Apply Three Bond Sealant to the secondary output shaft bearing housing; then install on the transmis- sion and tighten securely. Install the left and right transmission mounting brackets and tighten the cap screws securely.
The transmission is now ready to be installed on the V- belt housing. Center Components NOTE: This procedure cannot be done with the engine in the frame.
Complete Removing procedures for Top-Side, Left-Side, and Right-Side must precede this procedure. Rotate the crankshaft carefully until the second con- necting rod is at BDC; then using a large wooden dowel or hammer handle, carefully push against the first connecting rod until the piston/connecting rod assembly is free of the cylinder bore.
Remove the two cap screws from the second con- necting rod cap and remove the cap. Account for one bearing insert. Lightly rock the bearing caps in the saddles while applying pressure away from the crankshaft until the bearing cap is free of the engine block.
NOTE: The crankshaft should be supported in the three main bearing journal locations or stood on the flywheel end. Do not drop or strike the crankshaft. Set main bearing caps with inserts into the main bearing saddles and install cap screws. Finger tighten only. NOTE: Planing the engine block is not recom- mended as it will directly affect piston-to-cylinder head clearance. To determine if the cylinder deck can be planed, use the following procedure. Determine the maximum cylinder deck variation B.
Add the deck variation (V ) to the piston protrusion ) determined during removing (V ) to deter. DE398 DE363 DE356 DE362 10. Wash the crankshaft, connecting rods, and oil pan NOTE: Undersized connecting rod and main bear- and cover in parts-cleaning solvent; then dry with ings are available in 0.25 mm (0.010 in.) and 0.50 mm compressed air. Subtract the crankshaft journal measurement from the corresponding main bearing bore. The clearance must be within specifications. Install the main bearing caps and tighten to 44 ft-lb; then being careful not to mar the inserts, measure the main bearing bores using an appropriate inside DE609A micrometer/snap gauge. DE352 DE623 19.
Using an appropriate inside micrometer, measure the 22. Examine the piston pin bushing for galling or discol- inside diameter of the connecting rod bearing insert. If either condition exists, replace the bushing It must be within specifications or the bearings or or connecting rod. NOTE: Replacement pistons are only supplied as class A.
Class B and C are reserved for production engines. Replacement pistons are available over- sized by 0.50 mm (0.020 in.) and 1.00 mm (0.039 in.) and are supplied with piston rings. CAUTION Do not attempt to use standard rings on oversized pis- tons or oversized rings on standard pistons. DE431 DE377A 4. Apply a liberal amount of clean engine oil to the 7.
Remove the Main Bearing Seal Installation Tool or crankshaft main bearing journals and the main bear- shim stock; then install the main bearing cap screws. Ing saddles; then carefully install the crankshaft into the engine block. Rotate the crankshaft to make certain that no binding A. Place the oil expander ring in the 3rd (bottom) exists. Ring groove; then install the oil scraper ring over the expander making sure the oil scraper ring end 11. If pistons were removed from connecting rods, gap is not directly in line with the expander spring install the pistons onto the connecting rods making ends.
DE392 DE393A 17. Rotate the crankshaft so the crankshaft rod journal corresponding to the piston being installed is at bot- tom-dead-center (BDC). DE390 CAUTION NEVER force the piston into the cylinder.
If sudden DE335 resistance is encountered, remove and start over as 18. DE437 DE410 27. Install new O-rings on the oil sump and return pipes; then apply oil-soluble grease on the O-rings and place the oil pan into position.
Repeat steps 15-21 for the second piston. Install the oil pump (see Fuel/Lubrication/Cooling). Installing Engine/ Transmission NOTE: Arctic Cat recommends that new gaskets and O-rings be installed whenever servicing the ATV. NOTE: If the engine/transmission was removed as an assembly, proceed to Engine/Transmission in this sub-section. DE113A DE479 3.
Install the engine-to-transmission mounting plate and cap screws; then tighten the cap screws from step 2 and from this step to 35 ft-lb. Secure the driven pulley with a flat washer and nut (threads coated with green Loctite #609); then tighten the nut to 125 ft-lb. DE084B DE087A 3. Align and connect the rear propeller shaft to the rear 6. Install the cap screws, washers, and nuts in the left output drive flange and secure with four cap screws; rear, right rear, and upper right engine mounts. Then align and secure the front propeller shaft to the differential input flange.
Install the transmission level stick mount using a new O-ring; then connect the throttle cable and thread the throttle cable housing into the bracket. Install the muffler and secure to the exhaust pipe with two springs making sure the grafoil seal is in place. DE067A DE078B 15. Install the V-belt cooling fan assembly; then install the V-belt cooling boots to the V-belt housing. DE077C DE076A 16. Connect the V-belt cooling fan connector.
Connect the fuel supply and return hoses and secure with the hose clamps. Install the coolant filler neck on the thermostat hous- ing and tighten the hose clamp securely; then install the upper radiator hose. Tighten all hose clamps securely. Connect the shift linkage to the transmission shift arm and secure with the E-clip. Troubleshooting Problem: Engine will not start or is hard to start (White smoke present) Condition Remedy 1. Glow plugs not heating 1. Check and troubleshoot glow plugs 2.
Glow plug heating insufficient 2. Recycle glow plugs Problem: Engine will not start or is hard to start - smoke present (Compression too low) Condition Remedy 1. Problem: Engine idles poorly Condition Remedy 1. Valve clearance out of adjustment 1. Adjust clearance 2. Valve seating poor 2.
Replace - service seats - valves 3. Valve guides defective 3.
Replace guides 4. Rocker arms - arm shaft worn 4. NOTE: Special tools are available from the Arctic Cat Service Parts Department. Diesel Fuel Injection System The diesel engine in this Arctic Cat ATV is a “compres- sion ignition” engine. Extremely high pressure in the DE309A combustion chamber raises air temperature high enough 2.
2006 Arctic Cat 700 Efi 4x4 Se Service Manual
Locate the fuel solenoid mounted on top of the fuel filter head; then disconnect the spade connector from the solenoid. DE078A Unit Injectors DE647B 3. Remove the banjo-fitting bolts (A) and (B) and remove the fuel solenoid. Account for four crush To service the unit injectors, see Top-Side Components in washers.
CLEANING AND INSPECTING NOTE: Whenever a part is worn excessively, cracked, or damaged in any way, replacement is nec- essary. Remove the fuel level sensor and fuel pick-up screen.
Account for a seal. Completely drain all contaminated fuel from the fuel tank. Testing Oil Pump Pressure NOTE: The engine must be warmed up to the speci- fied temperature for this test (see Engine/Transmis- sion - Specifications).
Connect the Tachometer to the engine. Disconnect the oil pressure switch connector; then connect the Oil Pressure Test Kit to the oil pressure switch port. Remove the cap screws and nuts securing the radia- 6. Fill the cooling system with the recommended tor to the frame. Amount of antifreeze.
Check for leakage. Disconnect the fan wiring from the main wiring har- 7. Connect the fan wiring to the main wiring harness. NOTE: The fan wiring must be in the upper-right position.
Install the radiator (see Radiator in this section). REMOVING Water Pump 1. Remove the radiator (see Radiator in this section). Remove the fan assembly from the radiator.
Maintenance Charging NOTE: Arctic Cat recommends the use of the CTEK Multi US 800 or the CTEK Multi US 3300 for battery maintenance charging. Maintenance charging is required on all batteries not used for more than two weeks or as required by battery drain. Charging B. Emergency stop switch — engine will stop. NOTE: Arctic Cat recommends the use of the CTEK C. Reverse switch — reverse indicator light will illumi- nate. Multi US 800 or the CTEK Multi US 3300 for battery maintenance charging.
NOTE: If the meter shows battery voltage, the main NOTE: If the meter shows no battery voltage, trou- wiring harness is good; proceed to test the switch/ bleshoot the battery, fuse, switch, or the main wiring component, the connector, and the switch wiring har- harness. Engine Coolant Glow Plug Controller/ Temperature (ECT) Relay Switch/Thermistor The glow plug controller/relay is a plug-in device located under the seat. The glow plug controller/relay applies 12 The ECT switch/thermistor is a two-function device. One DC volts to the glow plugs in the pre-combustion cham- side is a normally open, temperature activated switch that bers to aid in cold starting.
Select the OHMS position on a suitable tester; then connect one tester lead to a suitable ground and the! WARNING other tester lead to the glow plug center connector.
Care should be taken to keep clear of the fan blades. The meter must read less than 1 ohm.
The meter must show less than 1 ohm resistance. If the meter reads open, replace the fuse.
NOTE: Make sure the fuses are returned to their proper position according to amperage. Refer to the fuse block cover for fuse placement. RELAYS The relays are identical plug-in type located on the power distribution module. DIODE (Starter Button) 4.
The meter must show less than 1 ohm. Turn the ignition switch to the LIGHTS position. NOTE: If voltage is not as specified, check the con- dition of the battery in the meter prior to replacing the 6. NOTE: If the meter does not show as specified, 8. Select Differential Lock on the front drive actuator switch; then connect the red tester lead to the white/ replace the front drive selector switch.
Orange wire in the supply harness. The meter must VOLTAGE show 0 DC volts.
Connect the red tester lead to the battery terminal; then connect the black tester lead to the starter sole- noid cable connection on the starter relay. The meter must show battery voltage. Install the inner splash panel, engine cover, and seat; then connect the negative battery cable to the battery.
INSTALLING NOTE: If voltage rises above 15.5 DC volts, the reg- ulator is faulty or a battery connection is loose or cor- 1. Place the alternator/regulator into position on the roded. Clean and tighten battery connections or engine; then secure with the existing hardware. Do replace the alternator.
Set the meter selector to the DC Voltage position. Set the meter selector to the DC Voltage position. Connect the red tester lead to one wire; then connect 2. Connect the red tester lead to the red/blue wire; then the black tester lead to the other wire.
Troubleshooting Problem: Charging unstable Condition Remedy 1. Battery connections loose or corroded 1. Clean and tighten connections 2. Alternator belt loose 2.
Tighten - replace belt 3. Alternator/regulator failing 3. Replace alternator assembly Problem: Starter button not effective Condition Remedy 1. The front drive actuator is located on the left side of the front drive input housing. With the engine stopped and Drive System/Brake the ignition switch in the ON position, a momentary System “whirring” sound can be heard each time the front drive selector switch is shifted.
INSTALLING 6. Turn the ignition switch to the ON position and check the operation by shifting the selector switch 1. Lubricate the O-ring on the actuator; then ensure that several times. All mounting surfaces are clean and free of debris. Remove the two brake calipers.
Account for the four cap screws. Pull the steering knuckle away from the axle.
Remove the tie rod cotter pins and discard the pins. Support the axle to not allow it to drop or hang. AF895D CAUTION 9. AF610D AG925 15.
Push the axle shaft firmly toward the differential to 18. Remove the lower differential mounting cap screw. Release the internal lock; then while holding the axle Account for a lock nut and washers. In, pull the CV cup from the differential.
CAUTION Do not attempt to use a slide hammer or differential/axle damage will occur. Place the differential on its right side; then remove it from the frame. Using a boot-clamp pliers (or suitable substitute), remove the boot clamps; then remove the boots and KX159 splined drive from the input shaft. Disassembling Input Shaft 4. GC011 GC011 2. Install the input shaft seal making sure it is fully seated in the housing.
AF984 GC014 3. Lubricate the input shaft with High-Performance #2 Molybdenum Disulphide Grease packing the boot ribs and splines; then assemble allowing excess grease to freely escape. CD112 GC015 2. Using a T-40 torx wrench, remove the cap screws securing the differential cover. Account for and make note of the ID tag location for assembling purposes. Place the pinion housing with new gasket onto the gear case housing.
KX175 KX181 5. Remove the left differential bearing flange assembly Disassembling Pinion Gear and account for a shim. Mark the shim as left-side. NOTE: Any service of the pinion gear or related bearings will require a new gear case/differential housing.
CC878 CC883 3. Secure the pinion gear in a bearing puller; then 2. Place the pinion assembly in a bearing puller; then remove the pinion bearing using a press. Account for install the bearing using a press. A collar and a bearing. NOTE: All bearings must be installed in the gear case and the pinion properly installed before pro- ceeding. Backlash NOTE: Always set backlash prior to any other shim- ming.
Install the existing shim or a 0.051-0.055-in. Shim on the gear case side of the ring gear assembly. GC033A GC039A 4.
Install the existing shim or a 0.063-in. Shim on the 6. Zero the dial indicator; then while holding the pinion cover side of the ring gear; then place the assembled stationary, rock the ring gear assembly forward and gear case cover onto the gear case and secure with back and record the backlash. Zero the dial indicator; then push the ring gear toward the dial indicator and release. End-play should be 0.004-0.008 in. To increase end-play, decrease the shim thickness.
To decrease end-play, increase the shim thickness. NOTE: Once proper backlash and end play are established, the gear case can be assembled (see Assembling Differential Assembly in this sub-sec- tion). NOTE: If a new housing is being installed, tighten the cap screws to 28 ft-lb.
Making sure the O-ring is properly positioned on the differential housing cover assembly, install the cover CD103 with existing cap screws (coated with green Loctite #609). CF278 AG925 4.
Install the inner fender panels. Install the front axles (see Drive Axles in this sec- Make sure the tool is free of nicks or sharp edges or tion). Damage to the seal may occur. Secure the upper A-arms with cap screws and lock 3.
Remove the wheel. Remove the cotter pin securing the hex nut; then remove the hex nut. Release the brake lever lock. AF896D KX041 5. Remove the two brake calipers (right side only). NOTE: Do not allow the brake calipers to hang from their cable/hose.
PR725A PR725A REMOVING FRONT DRIVE AXLE NOTE: For removing a front drive axle, see Front Differential in this section. CLEANING AND INSPECTING NOTE: Always clean and inspect the drive axle com- ponents to determine if any service or replacement is necessary. Remove the ATV from the support stand and release the brake lever lock.
Rear Gear Case INSTALLING FRONT DRIVE AXLE 1. Position the drive axle in the gear case and steering REMOVING knuckle; then insert the upper A-arm ball joint into the steering knuckle. Inspect the thrust button for excessive wear or dis- 3. Install the rear drive axles (see Drive Axles in this coloration. Inspect the bearings for discoloration, roughness, or 4. Install the left-side rear A-arms (see Rear A-Arms in excessive wear. Install the hub assembly onto the shaft.!
WARNING Arctic Cat recommends that only authorized Arctic Cat ATV dealers perform hydraulic brake service. Failure to properly repair brake systems can result in loss of con- trol causing severe injury or death.
CAUTION Brake fluid is highly corrosive. Do not spill brake fluid on any surface of the ATV and do not reuse brake fluid. NOTE: Whenever brake components are removed, disassembled, or repaired where brake fluid is exposed to air, drain all fluid and replace with new DOT 4 brake fluid from an unopened container. Inspect the brake pads for damage and excessive wear. NOTE: For measuring brake pads, see Periodic Maintenance/Tune-Up. Inspect the brake caliper housings for scoring in the piston bores, chipped seal ring grooves, or signs of corrosion or discoloration.
Making sure brake fluid does not contact the brake pads, compress the caliper holder toward the caliper and install the inner brake pad; then install the outer pad. CAUTION If brake pads become contaminated with brake fluid, they must be thoroughly cleaned with brake cleaning solvent or replaced with new pads.
Troubleshooting Brake System Problem: Braking poor Condition Remedy 1. Replace pads 2. Pedal free-play excessive 2. Replace pads 3. Brake fluid leaking 3. Repair - replace hydraulic system component(s) 4.
Hydraulic system spongy 4. Bleed hydraulic system - correct or repair leaks 5. Suspension The following suspension system components should be inspected periodically to ensure proper operation. Shock absorber rods not bent, pitted, or damaged. Rubber damper not cracked, broken, or missing.
Shock absorber body not damaged, punctured, or leaking. Front A-Arms REMOVING 1. Secure the ATV on a support stand to elevate the front wheels; then remove the wheels.!
WARNING Make sure the ATV is solidly supported on the support stand to avoid injury. Remove the cotter pin from the nut. Discard the cot- AF618D ter pin. AF616D AF610D 3. Route the brake hose through the upper A-arm shock CLEANING AND INSPECTING absorber mount; then secure the hose to the A-arm with the routing clamp.
NOTE: Whenever a part is worn excessively, cracked, or damaged in any way, replacement is nec- essary. AF618D CD008 8. Apply grease to the hub and drive axle splines; then 13. Install the wheel and tighten to 45 ft-lb (steel wheels) install the hub assembly onto the drive axle. Or 80 ft-lb (aluminum wheels). Remove the ATV from the support stand.
Rear A-Arms REMOVING 1. WARNING CD009 5. Secure the hub assembly with the nut.
Tighten only Use only Arctic Cat approved tires when replacing tires. Failure to do so could result in unstable ATV operation. The ATV is equipped with low-pressure tubeless tires of 6. CHECKING/INFLATING! Using an air pressure gauge, measure the air pressure in each tire.
Adjust the air pressure as necessary to Do not mix tire tread patterns. Use the same pattern type meet the recommended inflation pressure. On front and rear.
Failure to heed warning could cause poor handling qualities of the ATV and could cause excessive drive train damage not covered by warranty. Troubleshooting Problem: Suspension too soft Condition Remedy 1. Spring(s) weak 1. Replace spring(s) 2. Shock absorber damaged 2.
Replace shock absorber 3. Shock absorber preload too low 3.
Adjust shock absorber preload Problem: Suspension too stiff Condition Remedy 1. A-arm-related bushings worn 1. Remove the reinstallable rivets securing the steering post cover and remove the cover.
Steering/Frame/Controls 4. Unlatch the storage compartment lid; then slide the storage compartment cover assembly forward and lift off. The following steering components should be inspected 5.
Remove the four cap screws securing the handlebar periodically to ensure safe and proper operation. KX039 AL600D 9. Remove two cap screws securing the lower steering 2. Place the upper steering post bearings into the hous- post bearing flange to the frame; then remove the ings; then position on the steering post and secure the steering post.
NOTE: Compressing the brake lever several times will quicken the draining process. Install the steering post access cover and secure with reinstallable rivets; then install and secure the radia- tor access cover. Place an absorbent towel around the connection to absorb brake fluid. Remove the clamp screws securing the brake hous- ing to the handlebar; then remove the assembly from the handlebar. Gently press the brakelight switch into the housing (left to right) until the mounting tabs snap into the four locating holes.
AF677D AF680D 4. Remove the actuator arm and account for a bushing.
Place the two halves of the throttle control onto the Note the position of the return spring for installing handlebars and secure with the two machine screws. Install the instrument pod and secure with the rein- stallable rivets. Secure the ignition switch with the retaining ring. Use extreme care when removing the bearing. If the bearing is allowed to fall, it will be damaged and will have to be replaced.
AF759D PR264A 4. Apply a small amount of grease to the hub splines. Pump the hand brake lever; then engage the brake lever lock. Tighten the hub nut (from step 6) to the shaft.
Tighten to 200 ft-lb. DE047A AF786D 5.
Adjust the handlebar direction until the two measure- NOTE: The distances from the inside rims to the ments are equal; then secure the handlebar to the rear frame tubes should be equal. If the measurements rack using tie-down straps. Are equal, proceed to step 8. CLEANING AND INSPECTING NOTE: Whenever a part is worn excessively, cracked, or damaged in any way, replacement is nec- essary. Clean all rack components. Inspect all welds for cracking or bending.
Inspect threaded areas of all mounting bosses for stripping. CD666 CD691 2. Remove the seat. Remove the cap screws, shoulder screws, and lock nuts securing the front rack to the frame; then remove the front rack.
Account for the grommets and bushings. Remove three reinstallable rivets securing the right side panel. CD681 CD765 9. Rotate the handlebar to the full-left position; then lift 2. Connect the headlight connectors to the appropriate and slide the panel to the rear and lift the rear up to headlights and the front accessory plug wires to the clear the handlebar. CD779 CD782 7. Install the left-side and right-side splash panels and 3.
Remove the cap screws and flange nuts securing the tighten the cap screws securely. Install new nylon footrests to the frame; then remove the footrests. Ties in the appropriate locations. CLEANING AND INSPECTING 8. Remove one shoulder screw and lock nut and three plastic rivets (on each side) securing the rear body panel to the footwells. Slide the muffler rearward to clear the mounting lugs and remove the muffler. INSPECTING MUFFLER CD691A 3.
Taillight Assembly REMOVING 1. Unplug the three-prong connector and free the tail- light wiring harness from the frame. Remove the torx-head cap screws securing the tail- light assembly to the frame. Account for any wash- ers.
Remove the taillight assembly. CD690A INSPECTING 3. Troubleshooting Problem: Handling too heavy or stiff Condition Remedy 1. Front wheel alignment incorrect 1. Adjust alignment 2.
Lubrication inadequate 2. Lubricate appropriate components 3. Tire inflation pressure low 3. Adjust pressure 4. Tie rod ends seizing 4.
Replace tie rod ends 5.